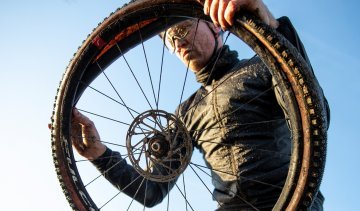
Bicycle inner tubes for road bikes or MTBs: Wha...
Bicycle tube or tubeless tyre? Butyl, TPU or latex? Find out which system is best for you and your bike here.
Perhaps you’re familiar with the basics, but do you want to learn more about the physics behind a wheel? Allow us to give you an in-depth explanation.
Wheels are one of the more impressive aspects of a bicycle. At a relatively low weight, they can withstand immense forces and are a decisive factor in defining your bike’s riding characteristics. If you would like to build custom wheels and go deeper into the process, or if you just want to better understand why system wheels are made with certain properties, we’ve put together some theoretical knowledge that is certainly worth considering.
We know of two fundamentally different types of bicycle wheel builds. Compression-spoked wheels follow the principle of wooden carriage wheels from the Middle Ages: the acting forces are supported by the hub via a few thick spokes pointed down towards the rim. This principle is still adhered to by most modern three-, four- or five-spoke carbon fibre wheels, as they are most often used in the triathlon or aero sector. However, the overwhelming majority of bicycle wheels are designed as tension-spoked (also called wired) wheels with a significantly higher number of spokes. The system mass and all driving dynamics are literally attached to the hub (the upper part) of the rim. Thus, the wheel offers an optimal weight-to-stability ratio.
Spokes made of thin wire are much stronger tension-wise than in compression. The rim, on the other hand, is quite pressure-stable. Tension spokes experience an elastic change in length while in use. That is why the spokes must be pretensioned enough to allow the system to compensate for short-term stretching. The spokes relieved at the lower part must not lift off from the rim base. Such loosening and re-tensioning would cause a notch effect between spoke bend and hub flange – and weaken the spoke at this point. For this reason, the preload must be as high and as uniform as possible. With sufficient pre-tensioning of all spokes, peak loads during sprints, jumps and full braking actions are distributed evenly over all spokes. Nevertheless, try not to go overboard with spoke tension. Carbon fibre rims in particular are somewhat sensitive in this regard during assembly, and are more likely to break than bend. So be sure to follow the manufacturer's instructions for hubs, nipples, spokes and rims, and use a tensiometer if in doubt, but especially if you are lacing carbon rims. Theoretically, the connection between spoke and rim makes the perpendicular wheel stable in itself, so that it can absorb vertical forces. In reality, however, the wheel must also withstand extreme torsional and lateral forces. The absorption of these forces is ensured by at least two hub flanges. The support on both sides results in the angle of the spoke discs, and can absorb high forces – comparable, for example, to the mast of a sail boat, which is held in place laterally by pre-tensioned shrouds. If one spoke breaks, the other spokes are initially able to compensate for the forces that occur. In the long run, however, this can lead to overloading of the neighbouring spokes, which is why the damaged spoke should be replaced as soon as possible.
The hub flange affords the spokes lateral support so that they can also withstand twisting in a horizontal direction. © bc GmbH
Various forces act on the wheel, and are in turn addressed by different wheel design features. Vertical forces act on the wheel when you get on your bike: this force is transferred to the hub via the dropouts in the frame, and thus hangs in the spoke lacing along the upper rim arc. Spokes pointing downwards are then slightly relieved. The degree of vertical force is strongest when you hit a curb or land a jump. Lateral forces strongly occur when cornering or when swaying, but also already during the sine wave pendulum motion which allows you to ride straight forwards. Your wheels absorb these forces using lateral support supplied by the spokes. Rear wheels in general and front wheels with disc brakes are asymmetrical, meaning the angles of the spokes are not the same on both sides. This is because the hub flange is indented to make room for the brake rotor or cassette. Since the rim must be centred over the hub, the tension of the spokes is automatically higher on the side with the more obtuse angle than on the side with the more acute angle. The wider your hub and the more acute the spoke angle, the more stable your wheel. The similarity of spoke angles and preload also contributes to stability, giving symmetrical wheels a clear advantage here. Asymmetrical rims help to create greater stability by shifting their centre towards the more acute spoke angles (i.e. to the left for the rear wheel, to the right for the front disc wheel). This way, the spoke angles are slightly adjusted and often you only need one spoke length. Torsional or rotational forces act on the wheel when you accelerate or decelerate. The amount of force your legs put into the crank via the chain comes into the hub body via the sprocket and the freehub and tries to turn the hub against the rim. The same concept applies to disc brakes (but also coaster or drum brakes), only in the opposite direction.
With radial lacing, the spoke is the shortest and most direct connection between the hub and the rim – its imaginary extension is aligned through the centre of the wheel axle. Radial wheels are therefore laterally stable and lightweight. When absorbing the torsional torques caused by acceleration or braking (disc brake, back-pedalling), radial storage is not very helpful, as it can only transmit small amounts of torsional force. That is why radial wheels are best suited for wheels without brakes (e.g. on a trailer) or as front wheels with rim brakes. The drive side of the rear wheel and the disc brake side on both front and rear wheels should therefore not be spoked radially. In order to better absorb rotational forces, the spokes must have flatter contact with the hub – ideally, at right angle to a line that intersects with the centre of the axis. The hub flange acts as a lever: the larger the flange diameter, the more stable the wheel. The ideal balance between weight and stability is offered by triple crossing, which is why it is most widely used on bicycles. The number of crossings indicates how many spokes a spoke crosses between the hub and the rim. In classic triple crossing, each spoke crosses its first, third and fifth neighbouring spokes. It is above the first two crossing spokes, but below the third.
In the past, very soft, thin rims were used for road bikes. The extremely high amount of pressure (10-12 bar) required by very narrow tyres (18-21 mm) that were common at the time compressed the rim – and thus reduced the spoke preload. As tyre widths slowly grew, the problem became less relevant: more modern rim shapes and better materials did one thing, wider tyres (23-25 mm) with correspondingly lower pressure (6-9 bar) did another. In the case of mountain biking, the phenomenon used to play virtually no role. Since the arrival of tubeless technology, however, tyres sit much tighter on the rim. The higher form fit of both components due to lower manufacturing tolerances improves the system’s airtight seal. However, as soon as the tyre is fully situated in the rim flange, it compresses the rim. As a result, the preload of the spoke is reduced, which is why tubeless wheels have to have a higher preload. Therefore, it’s important to take notice of the manufacturer's specifications on the system weight of the wheel, and pay attention to the corresponding air pressure range when choosing rims and tyres.
When you’re building custom wheels for your mountain bike, you can use different factors to influence whether the wheel should have maximum stiffness or a certain degree of elasticity. There are different philosophies here, which can also be found in system wheels. The approach transferred from motocross motorcycles to modern e-mountain bikes, for example, states that the rear wheel should be as stiff and wide as possible and may also be smaller, as it transmits the driving force and is exposed to higher lateral forces in corners, and should therefore be more agile. The front wheel, on the other hand, can be a little more "compliant" to provide maximum traction. That's why it's a little narrower and bigger. Many “mullet” wheel combinations, i.e. a 29 inch in the front and 27.5 inch in the rear, take this consideration into account as well as system wheelsets in the Crankbrothers Synthesis family. The opposite point of view argues for stiffer front wheels for maximum steering precision and somewhat more flexibly-designed rear wheels that better follow the ground surface. An extreme example of this philosophy was the first Mavic Crossmax Enduro wheelset with 24 spokes in the front and only 20 in the rear, developed in collaboration with Fabien Barel. To achieve full on compliance and targeted flex to maximize traction, Zipp has come up with the 3Zero Moto line, which features so-called single wall rims instead of the usual hollow rims, which allow the wheel to specifically twist around the nipple seat, increasing the contact area of the tyre to the ground. Zipp calls this ankle compliance in reference to the mechanics of the human ankle.
Only you can decide which approach is best for you and your riding style. And that's the beauty of an individually assembled wheel: You decide, within the framework of the physical possibilities, which criteria are important to you and can thus build the best wheel for you. You can find lots of tips on this in our other articles on wheel building: