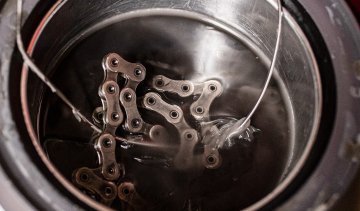
How to Chain Wax: Easy bike chain waxing guide
Chain wax ensures a clean, quiet, and highly durable bicycle chain. Whether it's hot wax or drip wax - we'll show you how to properly wax your bike chain.
Brakes are one of the most critical safety component on your bike, so you should pay close attention to them during maintenance.
Hydraulic disc brakes are subjected to significant forces and various external influences, requiring regular attention to ensure optimal performance. These systems contain several moving parts that need proper maintenance. The hydraulic system should be bled periodically and checked for leaks, and it's important to ensure the brake fluid remains clean. DOT brake fluid, in particular, absorbs water over time, which can degrade performance and necessitates routine replacement.
It's also crucial to avoid any contact between brake discs and brake pads with oil, as this can compromise their effectiveness. Additionally, the pads and discs must be correctly matched to work efficiently together. Regularly inspecting the wear on both the pads and discs is another key aspect of maintenance. As you can see, maintaining your brake system is essential to achieving maximum performance and ensuring safety. We strongly recommend conducting preventative maintenance rather than waiting for defects or noticeable performance drops to occur.
In this guide, we'll focus on exemplary brake maintenance for Shimano, SRAM, and Magura systems, as these are among the most commonly used. While the basic principles of brake maintenance are similar across manufacturers, there are some minor differences in procedures like bleeding and filling. These variations may also depend on whether you're working with mountain bike or road bike brakes.
Hold the brake caliper tight and get ready – with the red bleed screw, you’ll maintain your disc brake in no time!
Bleed your brake lever like a pro – with a funnel and mineral oil, you’ll get your disc brake back in top shape!
The required tools... © bc GmbH
...and a showcase workshop. © bc GmbH
To help you get everything ready and avoid searching for tools with dirty or oily hands, here’s a list of the tools and supplies you’ll need.
We strongly recommend using only the tools, bleeding kits, and fluids specified by the manufacturer for each brake system. Mixing components from different manufacturers can cause serious functional issues and will also void any manufacturer warranty.
Before working on the braking system, you’ll need to remove the wheels from the bike. However, before doing so, check the brake discs for any signs of warping. A warped disc can be identified if it "wobbles" sideways in the brake caliper when rotating. Minor warping is acceptable and can often be corrected using a truing tool. This may cause a slight pulsing sensation while braking, which is generally tolerable. However, if the warping is severe and prevents the brake caliper from being adjusted without rubbing, the disc may need to be replaced.
Next, inspect the friction surface of the discs. While the discs wear down more slowly than brake pads due to the hardness of the steel, wear still occurs over time. You can often detect this by running your fingernail along the transition between the friction surface and the carrier arms—if you feel a "step," it indicates thinning. Use a caliper to measure the exact thickness. If the thickness is close to or below the wear limit (typically printed on the disc), replacement is necessary.
Discoloration, such as reddish or bluish tones, indicates the disc has experienced high temperatures, likely during a descent. This is generally not a cause for replacement unless the disc appears entirely "burned out." Examine the friction surface closely for embedded fragments of pad material, which can occur when the pads overheat and bond with the disc. This indicates the pads have reached their thermal limit. If you’re using organic pads, consider switching to sintered metal pads, which are more heat-resistant.
It’s also a good idea to check the disc’s attachment to the hubs. Use a torque wrench to ensure proper tightness. Torque specifications are typically printed on the disc or the center lock ring. If no specifications are available, use 6–7 Nm for 6-bolt discs and 40 Nm for center lock systems.
If the brake discs are oily or heavily soiled, they must be cleaned. Use a standard brake cleaner sprayed onto a clean, oil- and grease-free cloth, and thoroughly wipe both sides of the braking surface. For optimal results, wipe the disc again with a water-soaked cloth, as brake cleaner can leave residues that reduce friction and temporarily impair braking performance.
If the brake discs are slightly warped, ... © bc GmbH
... they can be straightened with an alignment tool. © bc GmbH
Take a close look at the brake lines – this way, you’ll ensure your disc brakes work perfectly!
Brake hoses should be free of damage and securely connected. A visual inspection will typically reveal any significant issues. In some cases, internally routed hoses may rub against the inside of the frame if proper guides are not used—this is particularly common with aluminum frames. If you notice visible cracks or deep cuts on the hose, it’s time for a replacement.
Pay special attention to the connections, as this is where problems are most likely to occur. Look for any signs of oil leakage or a pinched hose that could indicate a fault. To inspect these areas thoroughly, pull back the rubber sleeve at the brake lever and, for Shimano systems, remove the protective cap from the bleed nipple on the caliper.
A thin, film-like layer of oil is usually not a cause for concern, especially if the brake’s pressure point remains defined and firm. Minor sweating of oil can occasionally occur on hot days. However, if you notice a drop of oil forming, this indicates a sealing issue. In such cases, the brake is not properly sealed, and the hose will need to be reconnected or replaced.
Shimano and SRAM both use a very similar retaining screw to secure the brake pads, which is held in place with a safety pin to prevent it from loosening. Magura is an exception: the MT5 brake pads (one-piece, connected by a bar) don’t require a retaining screw, as they are held by hooks, integrated in the caliper. As such, there is no option to install a screw. The two-piece pads of the MT7 and the 2-piston MT models, however, lack hooks and are traditionally secured with a retaining screw. If a safety pin is present, remove it first. Then unscrew the retaining screw, and the pads are free to be removed.
The pads can now simply be pushed toward the center and pulled out. With some calipers, it’s easier to do this from the top, while with others, it’s better from the bottom. This can sometimes be a bit tricky—just try and don’t get frustrated!
Take a close look at the pads from both sides: if you notice oil residue, it could indicate that the caliper is leaking at the piston. The caliper itself should also be dry. This can sometimes be hard to spot, but your phone’s flashlight is usually helpful here. Check the condition of the pads carefully. Is there still enough material left? If the pad thickness is significantly less than 1mm, you should replace them. Uneven wear could be a sign of a seized or sticky piston.
After removing the pads, you can use a cloth to wipe through the caliper and remove any coarse dirt or brake dust.
The pad retaining screw must be removed... © bc GmbH
... then the pads can be removed. Left: Old; Right: New. © bc GmbH
Before bleeding a brake system, it’s important to clean and mobilize the pistons, as brake- and trail-dust tend to settle into every crevice. Over time, this buildup can cause a piston to become sticky or, in the worst case, seize completely. For the best access, it’s recommended to remove the caliper.
Gently pull the brake lever a few times and observe the pistons in the caliper. You’ll quickly notice if they extend unevenly. However, don’t overdo it—without the resistance of the brake discs and pads, the pistons can extend too far, potentially causing them to leak. Follow the general approach shown in the illustration below. Once the pistons are extended, clean the sliding surfaces thoroughly using a toothbrush or cotton swab and brake cleaner. After cleaning, the pistons should extend more or less synchronously.
Blow away any loosened dust and dirt with brake cleaner, then carefully push the pistons back into place. Ideally, use a flat tool made of a soft material, like plastic or wood. Be cautious to push them back evenly and straight, avoiding any tilting. Once fully retracted, the pistons should sit flush with the inside of the caliper.
Caution: If the pistons are difficult to push back or resist movement, you may need to open the bleed screw at the brake lever to relieve pressure from the diaphragm inside the lever. In this case, a drop of brake fluid may escape from the bleed opening on the lever, which is completely normal.
Air bubbles in brake fluid naturally rise to the top—that’s simple physics. To assist with this process, position the brake, so the caliper is downward, and the hose is vertical to the ground. However, this ideal positioning is only achievable if the brake system is completely detached from the bike. When the hose is routed through the frame, this position isn’t possible. In such cases, we recommend placing the bike in a repair stand, ensuring the brake lever is as high as possible and the caliper is positioned as low as possible. If the system is detached, you can usually lower the caliper even further, making it easier to work on compared to when it’s fixed to the frame.
For optimal filling, adjust the brake lever on the handlebars so that the bleed screw and the reservoir beneath it are as horizontal as possible.
At this point, methods diverge: While the basic principles of hydraulic brake operation are consistent, the filling and bleeding process varies significantly between manufacturers and requires specific tools. Here, we divide the process by brand—Shimano, SRAM, and Magura - as these are the most commonly used systems. You can find links to the manufacturer’s instructions below.
Critical Note: Always use the brake fluid specified for your brake system! Shimano and Magura exclusively use mineral oil, while SRAM historically used DOT fluid for all brakes, but lately also started offering brakes that use mineral oil. Be certain of your brake type and use the specified fluid. We strongly recommend sticking to the original fluid from the manufacturer, as different mineral oils and DOT fluids have varying chemical compositions. Using the wrong fluid can result in serious performance issues or even complete brake failure.
The same advice applies to brake pads: always use original manufacturer accessories for the best performance and safety.
Set the brake lever to a horizontal position. © bc GmbH
Unscrew the bleed screw
Check the seal. Sometimes it gets stuck in the bleed port!
Funnel filled with mineral oil
Installation of the bleed block
Air bubbles rising in the syringe hose from the line
A 1/4 turn opens the fill port
Oil is pushed from bottom to top with the syringe
Air bubbles rising in the funnel from the line
Unscrewing the funnel with stopper from the brake lever
Tightening the bleed screw
Close the fill port (1/4 turn clockwise)
Very important: Use the correct fluid for your brake.
Loosen the pad contact adjustment screw.
Remove the bleed screw (Torx 10).
Syringe with DOT brake fluid at the brake lever.
SRAM brake caliper with inserted bleed block.
Unscrew the bleed screw.
Connect the syringe to the brake caliper.
The brake system is being filled.
Close the brake caliper again.
Rising air bubbles in the syringe hose.
The syringe for the brake lever is drilled at the 30 ml mark on the scale.
This guide allows the pad retaining screw to be turned for fixation.
Insert the bleed spacer and secure it with the pad retaining screw.
Removing the bleed screw on the brake caliper.
Removing the bleed screw (Torx 25)
Syringe with a hole and without a plunger on the brake lever.
Mineral oil rises in the syringe.
Air bubbles rise in the tube.
The last air bubbles are removed from the system using a vacuum.
The EBT bleed screw is gently screwed back in.
The brake caliper is sealed again. Attention: Do not introduce air into the system!
After removing the bleed block, you can reinstall the brake pads. Make sure that the spreader spring is correctly positioned and does not extend into the surface of the pads with its hooks. After bleeding, the piston gap is optimized for new brake pads with full material thickness, so we recommend installing new pads. However, if the old pads are still in good condition (more than 1/3 of the thickness remaining), they can also be reused. After all, we don't want to waste any material!
Make sure the spring is properly positioned. © bc GmbH
The brake pads are being reinstalled. © bc GmbH
The pad retaining screw is being reinserted. © bc GmbH
Now reinstall the pad retaining screw and insert the safety pin. Next, mount the brake caliper back onto the fork or frame, aligning it with the brake rotor. Tip: Tighten the caliper bolts just enough so the caliper is slightly loose and can still move slightly without torque.
Pull the brake lever firmly. This will automatically center and align the caliper with the rotor. While holding the brake lever, gradually tighten the caliper bolts alternately and gently, ensuring that the caliper doesn’t shift out of alignment as you tighten. This method usually provides a quick and accurate alignment, ensuring the caliper is centered and the pads don’t rub on the rotor.
If the gap between the rotor and the pads is very small and the rotor lightly brushes against the pads during rotation, it’s generally not an issue as long as there’s no noticeable braking effect. To confirm, rotate the wheel slowly and observe whether it slows abruptly. For example, Magura brakes typically have a smaller gap between the rotor and pads than Shimano brakes, which can sometimes result in minor rubbing.
Finally, tighten the caliper bolts to the specified torque. If no torque specification is provided in the manual, 7–8 Nm is a reliable guideline.
The pads can be roughened with sandpaper. © bc GmbH
It shouls look like this after roughening the brake pads
Your brake system is now ready for action. If you’ve installed new pads, they need to be bedded in to adapt to the brake rotor. While you can do this on the trail, exercise caution: With new pads, the brake has less than half of its usual stopping power, leading to significantly longer braking distances. Setting a defined braking point before a curve will also be challenging. Less experienced riders should perform the bed-in process on a downhill, low-traffic road or a dirt path to stay safe.
For proper bedding-in, avoid constant dragging of the brake. Instead, brake in short, firm bursts. Continuous braking can cause the new pads to overheat and glaze, rendering them ineffective.
To speed up the process, you can lightly sand the new pads with fine-grit sandpaper prior to assembly. This roughens their smooth surface, increasing the friction coefficient with the rotor and reducing the time needed for bedding-in.
Now you’re ready to hit the trails with freshly maintained brakes! Off to new adventures! If you have any questions about maintenance or accessories, feel free to reach out to our service team.