Acros Factory Visit - Nineteen hub production
High-quality bearing and hubs are Acros’ game. Everything they produce is made in Germany and to the highest of quality standards.
Acros is most known for their top-quality bearings. What most people don’t realize, is that Acros’ first product was a suspension fork, which they released in 1999. Wanted to expand their portfolio in the bicycle industry, Acros began making headsets. As a subsidiary of HWG, a rolling contact bearing manufacturer, moving into the headset business just made sense. Their headsets were first seen on OEM bikes from Rotwild and today, Acros’ assortment includes various bearings and components for bicycles.
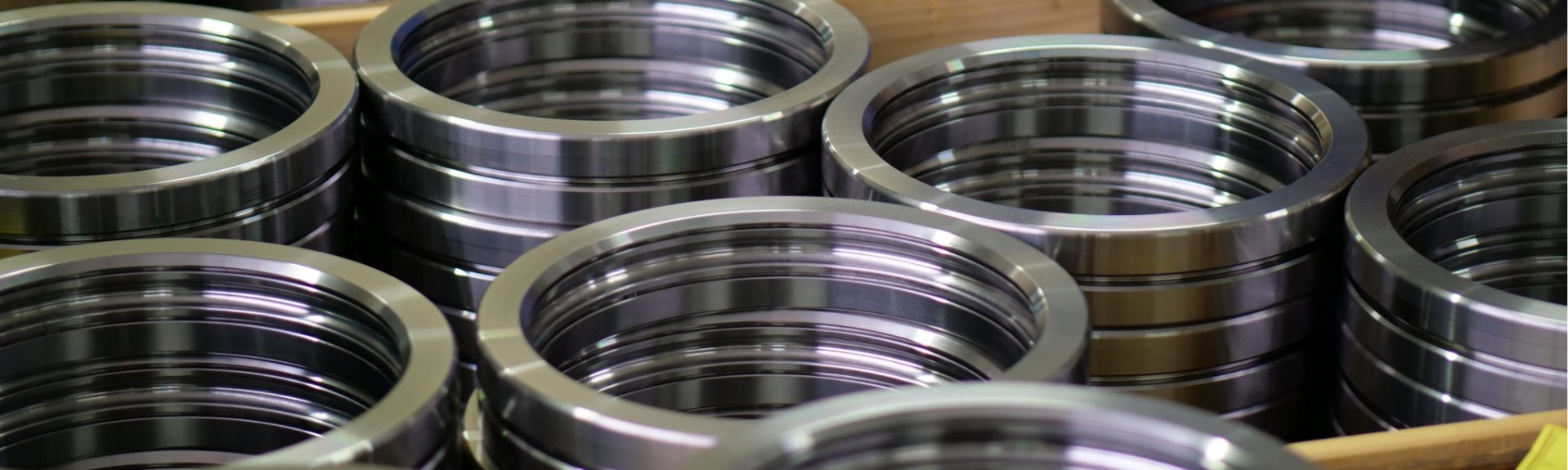
The outer bearing rings.
Made in Renningen
Acros’ newest products are their Nineteen hubs. Working closely with their holding company, HWG, Acros developed new state-of-the-art angular contact bearings for the Nineteen series. One of Acros’ defining features is their completely German production. Both the bearings and hub shells are developed, produced and assembled in Renningen in Southern Germany.

Getting the low-down.
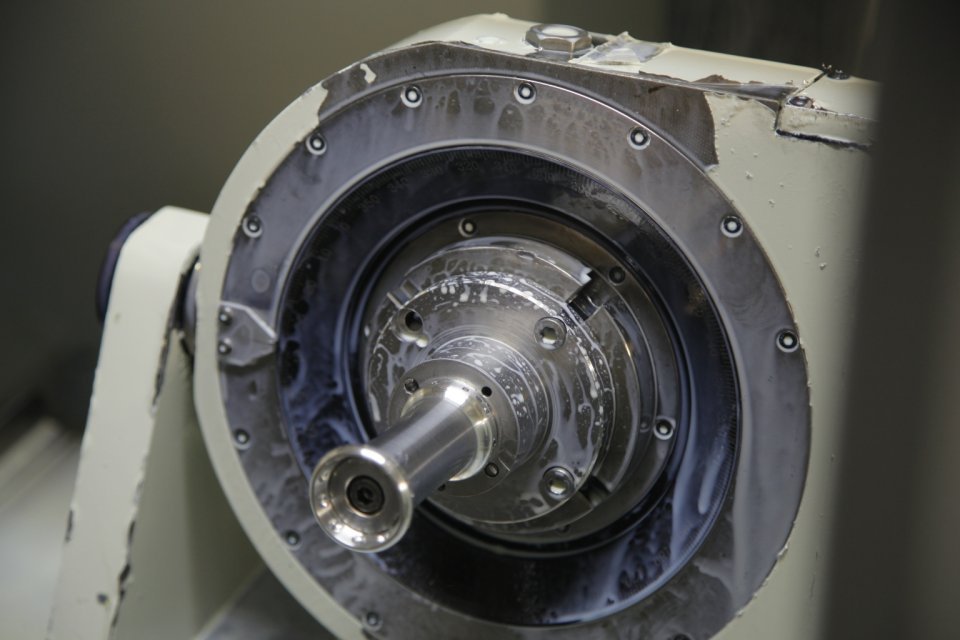
On to the lathe!
The Acros' factory
Wanting to see how Acros makes their new hubs, me and a few colleagues hopped in the van and headed south. The Head of Marketing, Alex, greeted us upon arrival and after a few refreshments we started the tour of the production facilities. Around 20 employees run the show here. The air is filled with the smell of shaved metal and cooling emulsion. The loud sound of CNC machines and lathes made it hard to hear, but Alex did a great job projecting that fact that every Acros hub is machined from a single block of aluminium. This process takes roughly 10 min per hub. After, the spoke holes are drilled, which takes an additional 2 min.
A part of hubs that require very precise machining are the ratchet freehub toothed washers. Because of the precision required Acros also makes these in house on their CNC machines to ensure top quality.
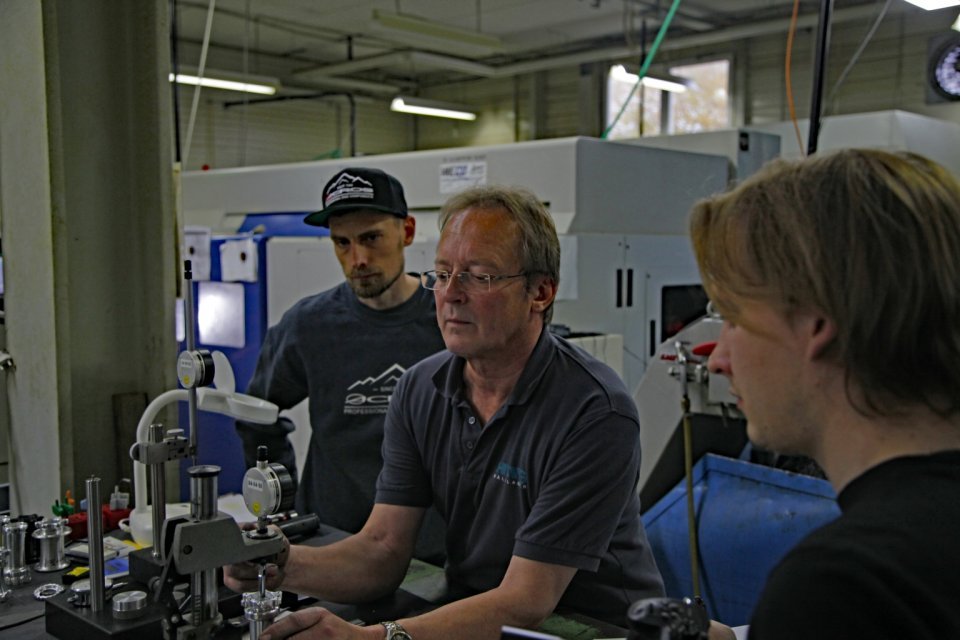
Every shell is tested for precision.
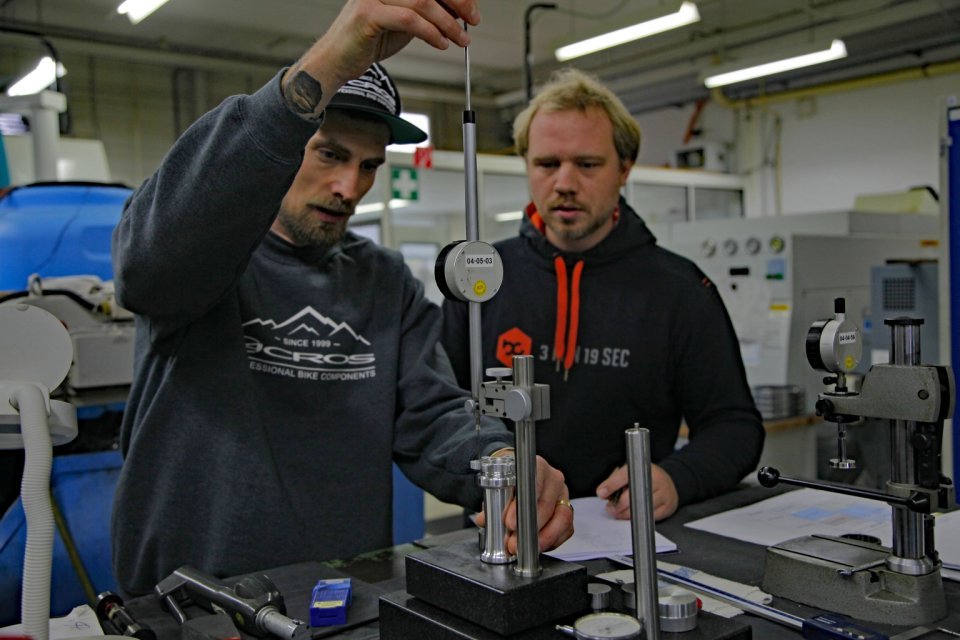
Seriously, every hub.
Final hub assembly
The final assembly of the Nineteen hubs is done by hand. The entire process takes about 15 min. and every hub is checked for smooth bearings and play.
Development
As mentioned above, all of Acros’ components are developed in Renningen as well. This allows them to take prototypes and test them directly in house. For example, seals are sprayed with saltwater steam for two days to make sure they are durable enough.
Final thoughts
Acros manufactures top-quality machined parts, and anything that has a bearing in it. They started with a fork, but landed in a different world, where they excel at German Engineering and know-how. For those looking for high-quality components, look no further than Acros.