bc visits Supernova’s HQ in Gundelfingen, Germany
Seeing Supernova’s high-quality production drove home the fact that they are truly market leaders when it comes to bicycle lighting.
Marcus Wallmeyer, founder and CEO of the premium bicycle light manufacturer, Supernova, invited us to see how their high-quality lighting is produced. A neat little fact, Supernova also turned twenty this year, just like us. Another reason for Benjamin, Rainer and I to head down and take a peek behind the curtain.
Humble beginnings
Before we begin, a little backstory. The first Supernova prototype light was developed by Marcus in his parents’ garage in 1995. An avid mountain biker since childhood, Marcus always had a problem finding a good light to ride with during the dark winter months. Every light he tried just didn’t hold up to the endurance style training he enjoys. Instead of just settling, he decided to build his own. The first version consisted of a motorcycle battery, halogen bulb and a tomato paste can. His long rides were again possible and with this prototype he participated in his first 24h marathon race. Other racers were super impressed by the light, and urged Marcus to start a company. In 1997, the first Supernova series model light with bottle battery hit the market.
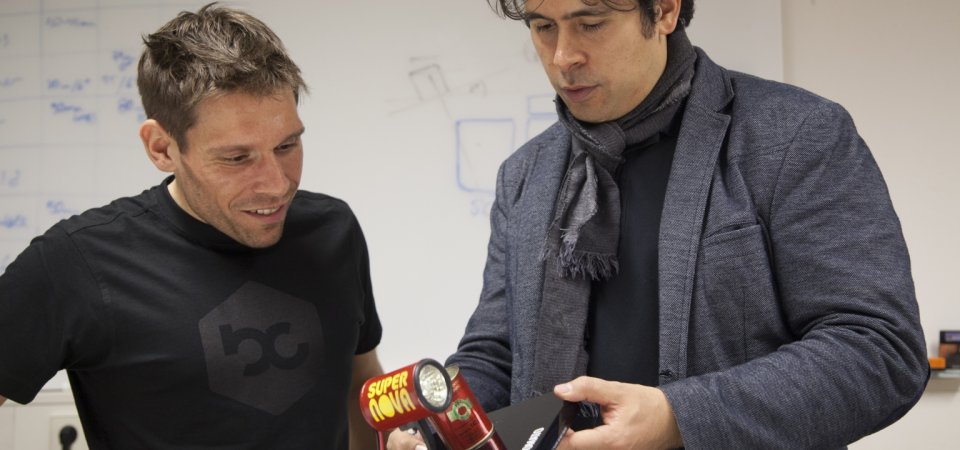
Marcus telling me more about the first Supernova light.
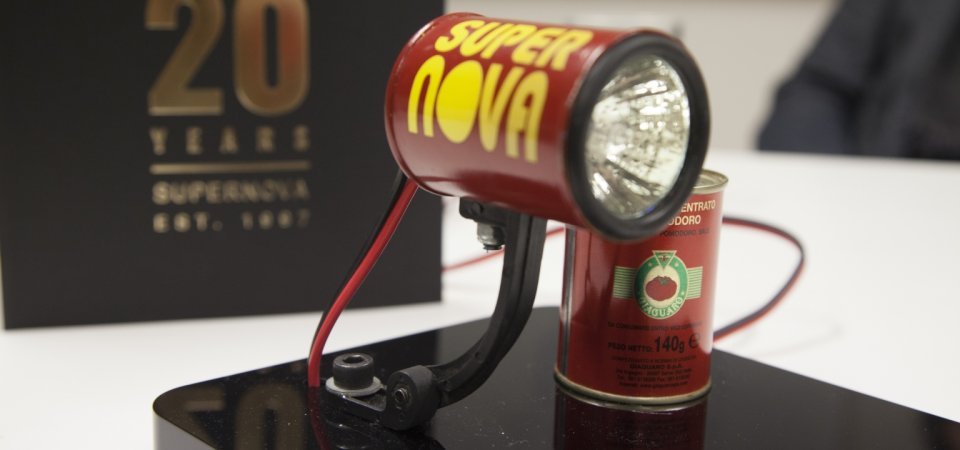
The light that started it all.
Southern German engineering
Supernova is located in Gundelfingen in the Breisgau region of Southern Germany. Their HQ looks simple from the outside, but once inside, the entire space exudes high-tech production. When we arrived, Marcus greeted us with the Sales Manager, Maximilian Franck. Of course, we had a cake with us to celebrate our shared 20 year anniversary. Over coffee, we discussed the origins of the company and Marcus’s continued enthusiasm for developing new products.
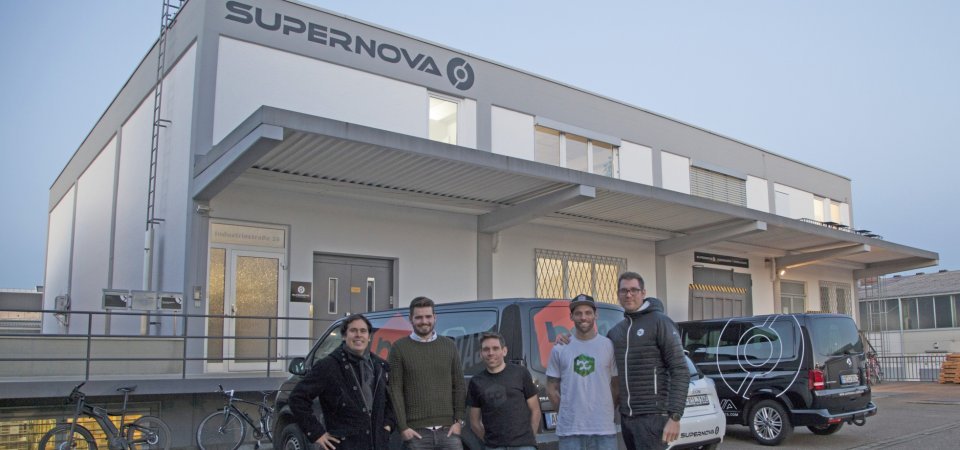
The Supernova HQ.
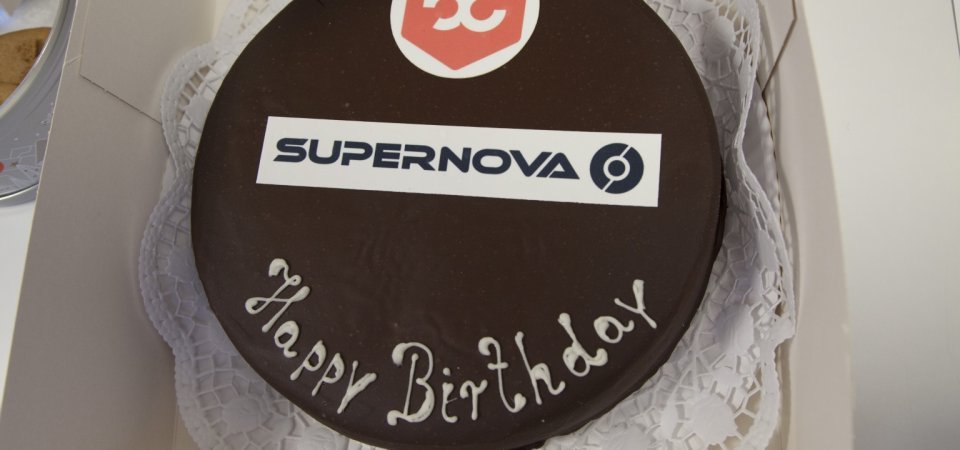
Birthday buddies!
Ideas and drawings
Through our discussion, we noticed all of the drawings and drafts of different products on Marcus’s desk. As a designer, he is constantly putting his ideas on paper or his iPad. Everything that is produced at Supernova is thought up and manufactured in Gundelfingen.
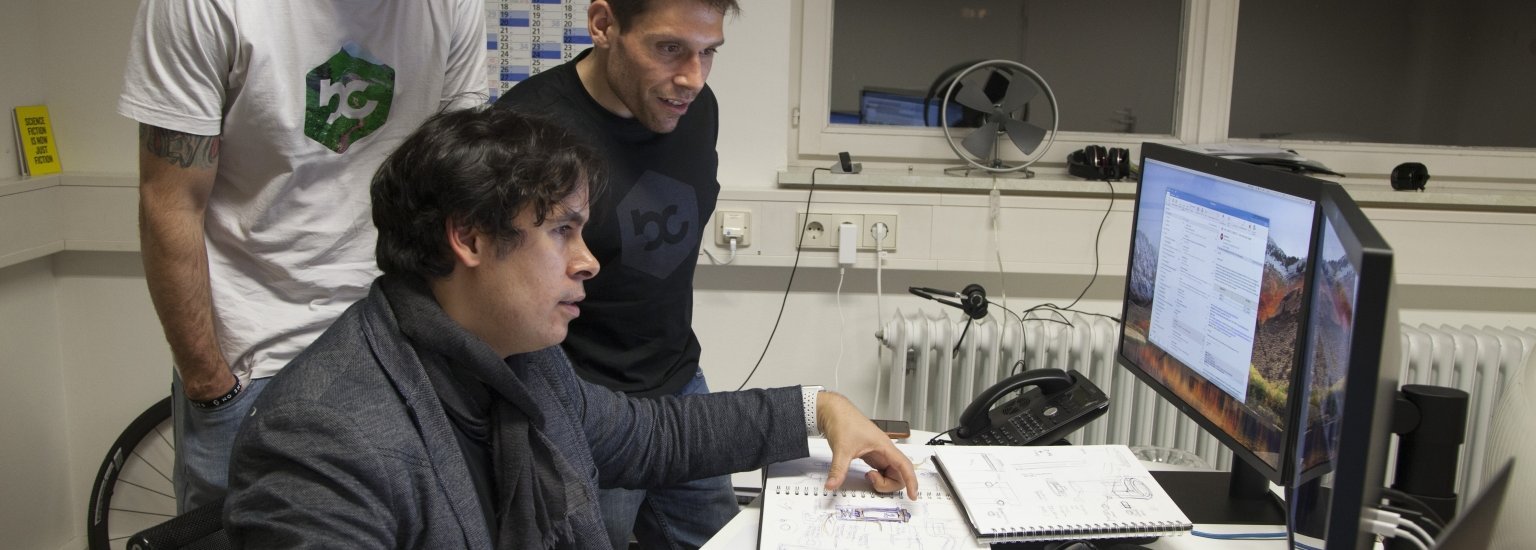
Marcus still does alot of drafting.
Their philosophy
Supernova focuses on product quality, attractive design and getting more people on the most eco-friendly form of transportation: bicycles. Many of the employees are cyclists themselves and it is easy to see how much of their hobby they put into their work.
Sustainability
Supernova also values sustainability, not only in their products, but in their day to day activities. The entire HQ runs off of green, eco-friendly power, a large part of their employees ride their bikes to work and if someone needs to use a car, Marcus has a fleet of electric cars for them. On top of that, all their products are PVC free and are made to last.
"A large part of their employees ride their bikes to work and if someone needs to use a car, Marcus has a fleet of electric cars for them."
Product design
Marcus has a degree in Transportation Design and it is easy to see in all of Supernova’s products. Each one has a distinct style that, while looking futuristic, offer a timeless feel.
Prototype production
After seeing where the ideas get put on paper, Marcus took us into the prototype production facilities. My colleague Rainer, who was an electrician, felt right at home among the sauntering guns, cables and LEDs. For the rest of us, we were still impressed by all of the individual parts we saw. Bastian, one of Supernova’s employees, then explained to us the various tests each prototype goes through and how they measure the light’s brightness.
Series production
Before we could go into the series production facilities, we had to discharge ourselves completely. Wearing special smocks and grounding shoe covers, we had to go through an ESD Check. This ensures that we are electronically neutral before stepping into the electro-sensitive production facilities.
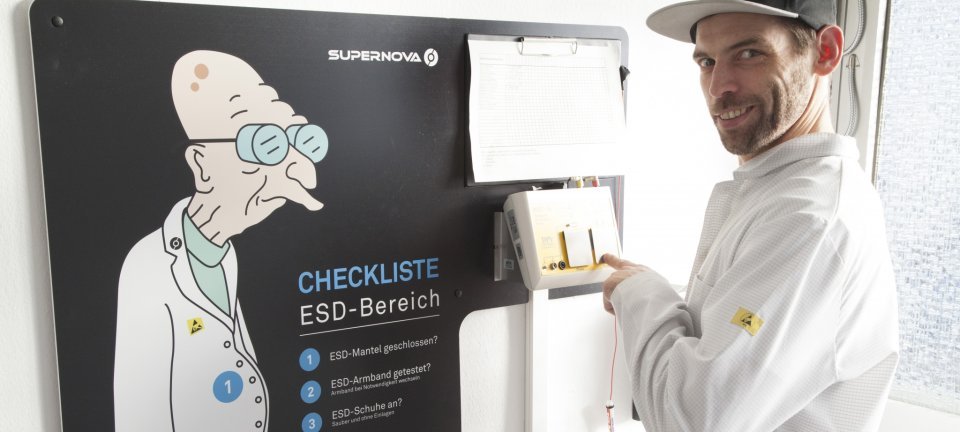
Rainer going through the ESD check.
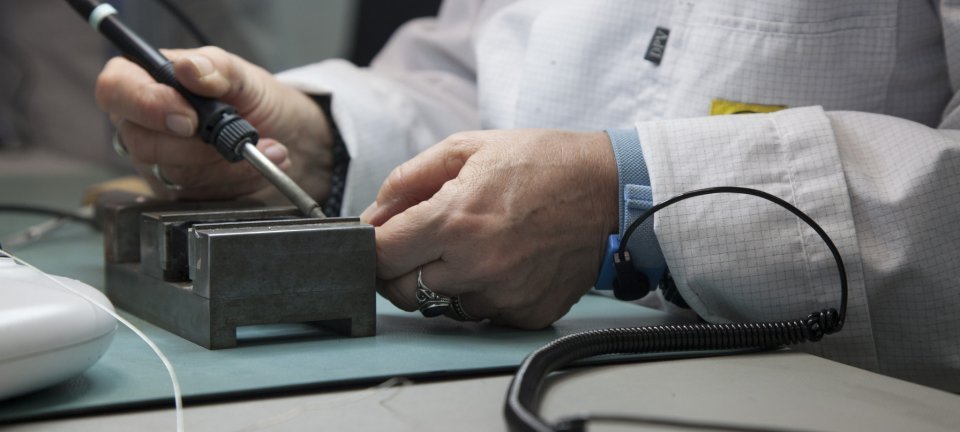
The ESD armband ensures that charges remain the same.
Once inside, Marcus showed us every part of the production process. We were surprised by how much manual work is done to each product. Every step along the way is documented carefully and tagged, becoming part of the serial number. This means if something goes wrong, Supernova can track if it was human error or if there was a material defect. They also offers a repair service, which in urgent cases can be taken care of within a 24 hour time frame.
Testing
All of Supernova’s lights are held to quality standards higher than that of what the industry requires. This means that everything is tested to military standards, so that their lights can withstand the harshest of conditions and be used for a least 10 years. Some of their test include salt water spray, annealing furnace and waterproofing.
It doesn’t get better than this
Supernova has always impressed us with their high-quality products, but seeing how they are produced made all the difference. Every light is largely put together by hand, and the attention to detail as well as the environment really blew our socks off. It is an honour to share a 20 year anniversary with such a great company. Here’s to another 20 years!