Visiting tune in Southern Germany
Lightweight bike parts are tune’s specialty. Add in their extreme level of quality control and you get the lightest most reliable products around.
One company that has always peaked my interest is tune. When it comes to German lightweight bike parts, they are the first that come to my mind. When I started putting tune parts on my bike, I began with their quick releases and with them I quickly fell into the weight weenie world. As soon as I could afford other parts, I added tune hubs, a seatpost clamp and a stem to my bike as well.
So when I heard that we had a chance to go see how tune’s parts are manufactured in Buggingen, Germany, I didn’t hesitate and set the date. My colleagues Benjamin, who wanted to see how his new tune wheelset is built, and Rainer were equally pumped and decided to accompany me.
Buggingen in Breisgau, Southern Germany
tune parts are known for their Olympic successes and have even found their way onto the Russian MIR space station. With this kind of reputation, one expects a big flashy office / production facility, but no, tune keeps it simple and could pass as a small German craftsman shop. The first sign of their hands on approach to their high-end lightweight components. As soon as we arrived, we jumped out of the car and were greeted by Harry, the sales manager and Sebastian, the CEO.
High-end craftsmanship
After checking out the machine where Uli Fahl, the founder, created his first quick release skewers almost 30 years ago, we headed into the main production facility. For those thinking we would find robots and an entire factory floor full of machines, you will search in vain. The place looked more like a machine shop than anything else, and I mean that in a good way. When you walk in, you know that a lot of what goes on here is done by hand. While there are high-tech refined machines, there are also people who know exactly how to use them. Everyone here is a craftsman, who is versed in their trade. We also saw each of the employees’ personal bikes just waiting to get out and ride after work. It’s always great to know those manufacturing the bike parts also ride themselves.
Raw metal to hub
Even though tune first hit the world stage with their quick releases, today they are best known for their hubs and wheels. Every tune hub starts off as a three metre long aluminium alloy slug that weighs roughly 25 kg. How the alloy is made is top-secret and only a few tune employees know the exact details. The special material and its strength allows tune to take a 1 kg block and machine it down to a 70 g hub body.
How the alloy is made is top-secret and only a few tune employees know the exact details.
This all happens in a CNC machine that is as large as a small car. A Kong hub is machined in roughly 6 min. and straight pull hubs take around 13 min. It’s meditative to watch how the CNC machine works and the precision it uses to lathe out each feature of the shell. After machining, each hub is manually checked for inconsistencies and even the slightest variances are sorted out. tune is known for their quality and every single product is held to the highest of standards.
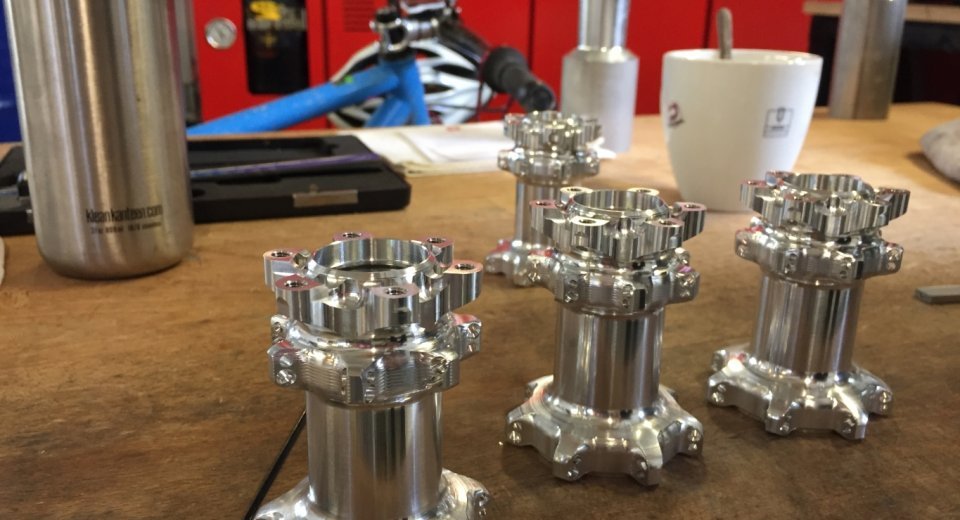
Ohh the beauty!
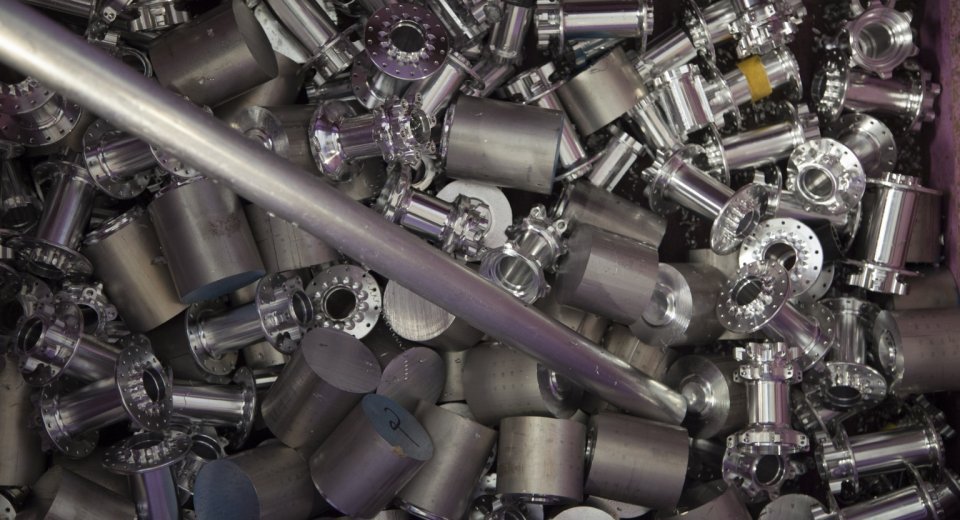
If a part doesn't meet tune's standards, it is thrown out.
Polishing
When the hubs pass the quality control check, they need to be deburred and polished. This is done in a barrel finishing machine, which as the name suggests looks like a barrel and is filled with ceramic particles that polish the hubs. This part of the process may seem bland, but tune has spent years adjusting the process to get perfect results.
Anodizing
The polished hubs are sent off to an anodizing specialist so they can get those beautiful tune colours. The only reason tune does this is because they cannot fulfil the environmental requirements needed to be able to anodize. After anodizing the hubs are then laser engraved back at the tube HQ.
Assembly
The finished hub shells are then ready to be used. Depending on their use, the proper axles, bearings and freehub bodies are installed. After, the hubs can be laced. The room where this is done is full of coloured nipples, spokes and rims. A place of beauty for those who like to lace wheels.
Wheel building
Each hub is first paired with the proper rim. The lacing itself happens either by hand or in a lacing and truing machine. All of their higher-end wheels, mostly those with carbon rims, are done by hand. For over 20 years, the same talented set of hands from Marzena Laba Petras have been spoking perfect wheels from hub and rim.
tune hand checks every wheel and makes adjustments where necessary.
All the other wheels have their spokes threaded into the hubs and then a lacing machine helps screw on the nipples. Afterwards, the wheels are put into a truing machine to centre them. Of course, tune hand checks every wheel and makes adjustments where necessary.
Development & Testing
Before a product is graced with the tune name, it goes through a very long development and testing process. A while back, the entire production facility used to be shut down for a few weeks a year, just to try out prototypes. Nowadays, tune has separate development and testing facilities. Of course these parts of the production were kept secret.
All tune wheels are also tested in Buggingen. For this purpose, they have quite a few testing machines that can bring the wheels to their breaking point. All of tune’s wheels are tested according the UCI impact standards and tune is always looking for ways to improve.
Born in the black forest – built to enjoy nature
tune’s motto really hits it home. Their products come straight from the Black Forest, with everything happening in Buggingen. It’s clear to see how much craftsmanship and quality is put into each of their products, especially their wheels. Having the chance to see tune’s facilities after spending years enjoying their products myself was an honour.