bc zu Besuch bei tune
Wir waren bei tune im Breisgau und haben uns angeschaut, wie in der kultigen Leichtbauschmiede ein Laufradsatz entsteht.
Eine der Firmen, die mich seit jeher begeistern, ist tune. Keine deutsche Firma ist wohl so untrennbar mit dem Thema Leichtbau verbunden wie tune. Die Schnellspanner der Leichtbauschmiede waren die ersten Teile, welche ich mir noch zu Schulzeiten leistete und die mir den Weg in die tune-ing Welt ebneten. Schnell war ich dem Leichtbauwahn verfallen und so kamen nach und nach auch Naben, Sattelklemme und Vorbau der Breisgauer Edelschmiede an mein Bike.
Als wir also die Möglichkeit erhielten, die Produktion vor Ort zu bestaunen, haben wir keine Sekunde gezögert und haben uns aufgemacht ins beschauliche Buggingen. Mein Kollege Benjamin liebäugelte schon länger mit einem Satz tune Laufräder und so entschloss er sich kurzerhand dazu, mitzukommen und sich anzuschauen, wie seine Laufräder von der Nabe bis zur Einspeichung hergestellt werden.
Buggingen im Breisgau
Die Parts von tune sind international bekannt und haben von Olympia bis hin zur Weltraumstation MIR überall Anwendung gefunden. Wir erwarteten also einen großen Firmenkomplex samt Bürogebäude, schicker Architektur und Glasfassade, die mindestens so stylish ist wie die Bikeparts von tune. Weit gefehlt, im kleinen Örtchen Buggingen sitzt die Firma in einem Gebäude, welches auch als kleiner Handwerksbetrieb durchgehen könnte. Wir mussten also zweimal hinsehen und ja, wir waren richtig! Voller Vorfreude sprangen wir aus dem bc-Bulli und wurden direkt herzlich von Vertriebsleiter Harry und Geschäftsführer Sebastian empfangen.
High-End in Handarbeit
Vorbei an der Maschine, auf der Uli Fahl vor knapp 30 Jahren die ersten Exemplare der weltberühmten Schnellspanner fertigte, ging es dann auch gleich in die Produktion und der Eindruck des klassischen Handwerkbetriebs bestätigte sich: Große industrielle Fertigungsstraßen mit Robotern oder Ähnlichem sucht man vergebens. Vielmehr ähnelt alles der Schlosserei, in der ich zu Schulzeiten arbeitete, um mir das Geld für die ersten tune-Parts zu verdienen. Offensichtlich fahren hier auch alle Mitarbeiter selbst Fahrrad, hier stehen die Bikes der Mitarbeiter sogar neben den Fräsmaschinen und warten sehnsüchtig auf ihren Einsatz auf der Feierabendrunde.
Vom Rohstoff bis zur Nabe
Auch wenn tune durch die Schnellspanner seinerzeit Weltbekanntheit erlangt hat, zählt der Bau hochwertigster Laufräder in Handarbeit mittlerweile zu den absoluten Steckenpferden der Firma. Im Zentrum eines Laufrads steht die Nabe und die bunt eloxierten Naben von tune kennt jeder. Ausgangspunkt einer jeden tune-Nabe ist ein drei Meter langer Alu-Rohling, der über 25 kg wiegt und so gar nicht an das Endprodukt erinnert. Aus einem 1 Kilogramm schweren Aluminiumblock wird im Anschluss der 70 Gramm schwere Nabenkörper gefräst. Dies geschieht in einer CNC-Fräse groß wie ein Kleinwagen. Eine Kong-Nabe wird hier in knapp 6 Minuten gefräst und eine Straightpull-Nabe fällt nach 13 Minuten aus der Maschine heraus.
Es hat schon beinah etwas Meditatives, wenn man sieht, mit welcher Präzision hier aus einem Block Aluminium ein kleines Kunstwerk entsteht.
Trotz präzisester und modernster CNC-Technik werden alle Nabenkörper noch manuell auf Maßhaltigkeit überprüft und bei minimalsten Abweichungen landen diese in der „Kiste des Mitleids“, wie Werkstattleiter Friedhelm sie nennt. Mitleid aus dem Grund, weil jede der dorthin verbannten Naben tadellos ihren Dienst verrichten würde, doch minimalste Abweichungen entsprechen nicht den Qualitätsstandards, die tune an seine Produkte stellt. 100 % Qualität steht hier an oberster Stelle.
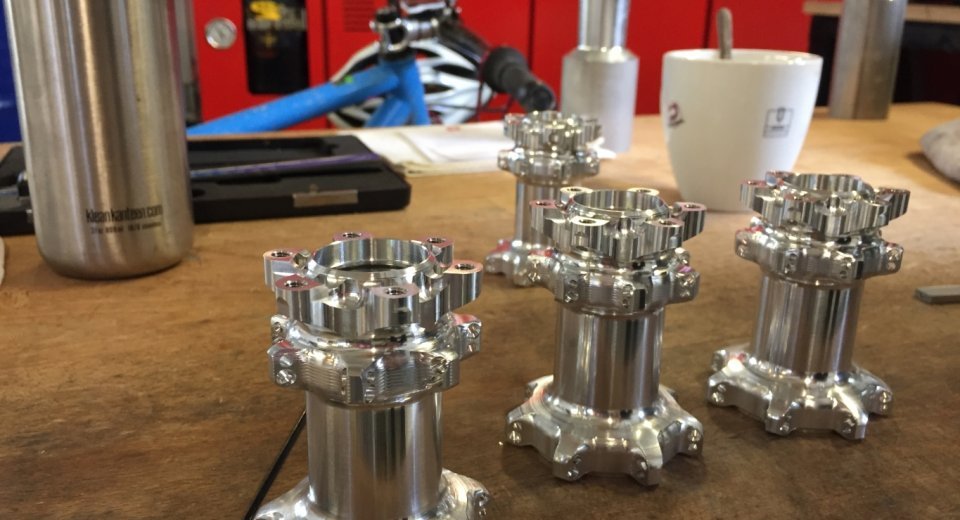
Optisch tadellos, doch die Qualitätskontrolle haben diese Exemplare nicht bestanden.
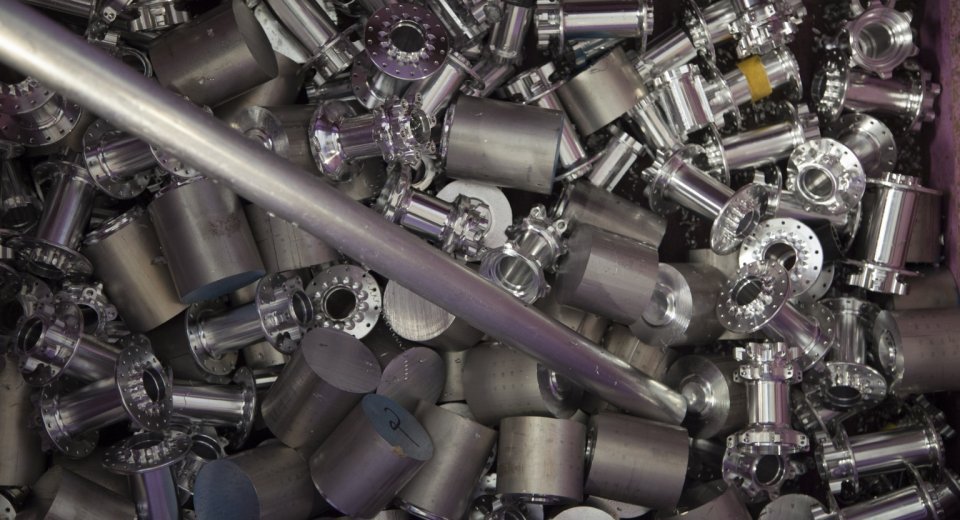
"Die Kiste des Mitleids"
Glanzkur
Nach dem Fräsen müssen die Naben noch entgratet und auf Hochglanz gebracht werden. Dies geschieht in einem sogenannten Trowalisierer. Das Gerät, optisch eine Mischung aus Betonmischer und Gulaschkanone, ist mit kleinen Reibkörpern gefüllt, welche die Naben entgraten und auf Hochglanz polieren. Dieser Arbeitsschritt, welcher auf den ersten Blick recht banal wirkt, hat bei tune jahrelanges Feintuning erfahren und ist laut Werkstattleiter Friedhelm eine Wissenschaft für sich.
Farbkur
Die auf Hochglanz polierten Naben werden im nächsten Schritt nun so schön bunt, wie man sie kennt. Im Gebäude selbst wird nicht eloxiert, da die Umweltauflagen für tune kaum zu erfüllen wären. Daher greift man auf einen spezialisierten Fachbetrieb zurück, bei welchem die Eloxalschicht in den bekannten Farben aufgebracht wird. Nun ist der Rohling beinahe fertig, es fehlt nur noch der Schriftzug. Dies geschieht wieder bei tune, wo die Nabe per Laser beschriftet wird.
Endmontage
Der fertige Rohling wird nun eingelagert und wartet auf seinen Einsatz. Nun werden also je nach Bestimmungszweck die jeweilige Achse, Lager und der gewünschte Freilauf montiert, bevor es in die Laufradfertigung geht. In großen Regalen lagern hier Abertausende von farbigen Nippeln, Speichen und Felgen. Ein wahres Eldorado für Laufradbauer und Tuningfreaks!
Laufradbau in höchster Präzision
Nachdem eine Nabe auserkoren wurde und die für sich passende Felge gefunden hat, geht es zum Einspeichen. Dies geschieht bei tune entweder von Hand oder in einem Einspeichautomaten. Alle High-End-Laufräder, größtenteils mit Carbonfelgen, werden komplett von Hand aufgebaut.
Seit gut 20 Jahren ist das die Spezialität von Marzena, die mit unglaublicher Präzision die edlen Naben mit den Felgen zu perfekten Laufradsätzen verbindet.
Alle anderen Laufradsätze werden von Hand „geigelt“, also die Speichen in die Naben eingehängt, und im Anschluss geht es in den vollautomatischen Einspeichautomat. Dieser produziert Laufräder mit perfektem Rundlauf, doch tune wäre nicht tune, wenn nicht auch die automatisch eingespeichten Räder noch von Hand kontrolliert werden würden. Jedes Laufrad wird so nochmals nachkontrolliert und bei Bedarf bis zur Perfektion nachzentriert.
Entwicklung & Testverfahren
Bevor es ein Produkt jedoch verdient den Namen tune zu tragen, durchläuft es eine lange Entwicklungs- und Testphase. Früher stand die Produktion jährlich einige Wochen still, um die Produktionsmaschinen für die Prototypenentwicklung zu nutzen. Mittlerweile gibt es jedoch eine eigene Entwicklungsabteilung und so kann flexibel entwickelt und getestet werden. Wir waren natürlich heiß darauf zu erfahren, was in Zukunft so an Neuigkeiten von tune auf den Markt kommt, leider wurden diese jedoch im „Geheimschrank“ vor unseren neugierigen Blicken versteckt.
Alle tune-Laufräder werden auch in Buggingen getestet. Dazu hat die Firma eigene Prüfstände angeschafft, die nach höchsten Standards die Produkte an ihre absolute Belastungsgrenze bringen. Dabei übertreffen die Laufräder alle UCI-Impact-Standards um ein Vielfaches und man versucht ständig die Ansprüche an die eigenen Produkte noch höherzuschrauben.
Born in the black forest – built to enjoy nature
Der Leitspruch von tune trifft es auf den Punkt: die Produkte stammen tatsächlich vollständig aus dem Schwarzwald. Von der Entwicklung bis zur Produktion in Buggingen steckt ein riesiger Anteil Handarbeit in allen Produkten. Tune betreibt keinen Modellbau, tune produziert haltbare, schöne Hochleistungs-Bikeparts für die Straße oder den Trail – „built to enjoy nature“ eben.