
DT Swiss is one of the leading manufacturers of wheels and rims. This success is not a coincidence. Painstaking and meticulous development, a lot of know-how from years of experience and an all-consuming passion for cycling come together to create perfectly harmonising products. These will deliver reliable performance at the highest level. Due to the innovative capacity, the wheels manufacturing specialist from Biel is known for its benchmark setting products. The result of which is tangible in their premium high-tech components for MTB, road bikes, gravelbikes and E-mountain bikes.
With the 240 DEG, DT Swiss has introduced its first high engagement hub. An extremely finely indexed ratcheting mechanism provides 90 engagement points per revolution. This means the hub has a maximum "freewheeling" of 4°. For you, this means more efficient power transmission and the ability to more delicately control the rear wheel drive on technically challenging climbs. And the best part: The sound! But, we can't easily describe that - you've got to hear it!
More about DT Swiss

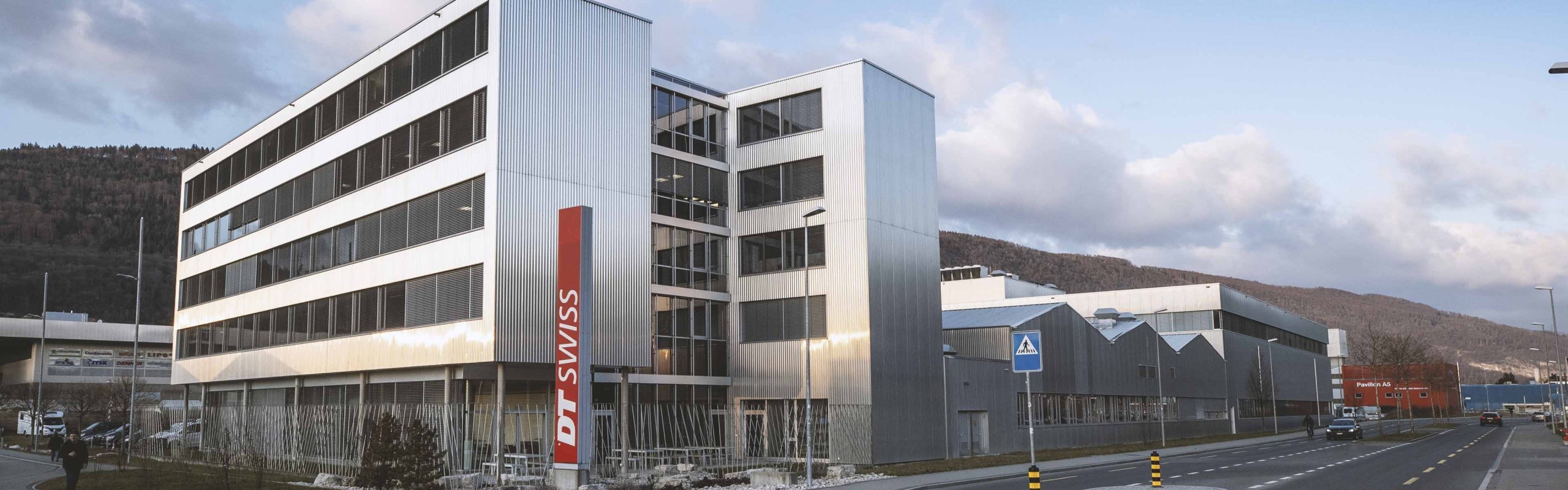
From a cyclist’s point of view, it is fortunate that this story is not a fairy tale, but reality. How else would we be able to experience the joy of riding DT Swiss wheels? Or feel the performance of a DT Swiss suspension? We also would not have such a vast selection of spokes for the different load requirements of the various cycling disciplines. And because we wanted to know whether bicycle spokes can also be used to replace cheese fondue forks, we decided to visit DT Swiss at their headquarters in Biel. A quarter of DT Swiss's 800 employees worldwide work there. In addition to the management, including the marketing and sales departments, the entire product development, spoke production facilities and the so-called Biel Performance Manufacturing, or BPM for short, are located at the home base.
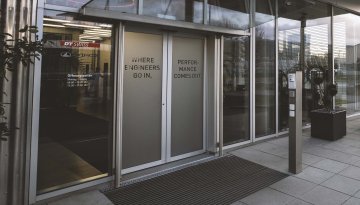
BPM: Not beats per minute, but best performance manufacturing expertise for wheels
The BPM is a scaled down production for wheels, mimicking the processes used at the company’s own main production facilities in Poland and in Taichung, Taiwan. At the BPM, DT Swiss develops the entire production process of the wheels in a small team of experts – and the know-how gathered here is used to train the employees at the production facilities. This sounds quite industrial and explains, at least in parts, the high quality of DT Swiss wheels – but a closer look reveals that beneath this exterior lies a deep-rooted passion for cycling: The leader of the BPM team, Marcel Waldmann, has been taking part in downhill MTB races for the last 29 years and evidently is an expert for wheels. He is a multiple Masters Downhill World Champion and has only wrecked five wheels in his entire career! What an unbelievable statistic! We saved ourselves the embarrassment of asking what his wheel brand of choice is...
Speech is silver, spokes are black...
Until 1994 only silver spokes existed, apart from a few painted exceptions. But then DT Swiss developed the so called “blackening” process, during which a chemical treatment colours the spokes black permanently. It goes without saying that no weight is added. This marked the first in-house development by the young company. Nowadays, roughly half of all spokes produced by DT Swiss leave production in the conventional silver of the raw material (18/10 stainless steel). The other half is blackened using the chemical process mentioned above or individually painted.
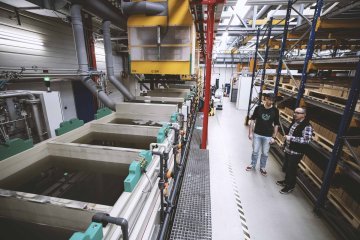
Spokes from Biel, produced by machines from Aachen
Admittedly, some local patriotism got the better of us. We noticed that the fully automated machines, which produce the 131 different types of spokes that DT Swiss has to offer, originate from Aachen. It all starts with the automatic alignment of the raw material, which is 5 km of wire wound around a roll. Next, the shaping of the spoke head and thread, and also the typical DT Swiss blading appear to happen in one go. This happens for all spoke types – straightpull or J-bend –and every spoke length. For butted, in other words, spokes which are thinner towards the middle, the wire is compacted in a cold forging process. The cold forging process results in a hardening of the material without weakening the structure, while also maintaining the elasticity of the steel. The flat-forged Aero spokes by DT Swiss go through an additional cold forging step: They are brought to their final, flat and thus more aerodynamically efficient blade shape with the help of 250 tonnes of pressure.
Destruction in the name of development
Generally speaking, the heart of a bike components lover bleeds at the sight of a testing laboratory, such as the one run by DT Swiss. But the wanton destruction of many components which takes place at these facilities, on which test engineer Philipp Lüdi keeps a close eye with his team of four, has a purpose: test the prototypes of high-end, precise and strong bicycle components. DT Swiss does not send a single wheel into production if it does not pass this internal test cycle, which is permanently optimised. This provides the testing standard for the development of newer, even better products. During this process the engineers go far beyond the usual testing standards: DT Swiss uses a pressure of 22 to 25 bar, for the pressure tests of rims. The ISO standard is only a fraction of these values and is considered to be questionable internally at DT Swiss...
Passing the culinary test
By the way, – to all the Swiss out there – we managed to experience the culinary delights of a hearty Swiss cheese fondue. And yes, it works! It is indeed possible to skewer a piece of bread on a spoke and guide it through the cheese following a figure of eight. The classic J-bend spokes provide an advantage in this scenario though their small barb from the bent spoke head, compared to the straightpull spokes. Otherwise, the shape – butted or not and bladed or round – is clearly a matter of taste. Just like choosing your wheels.
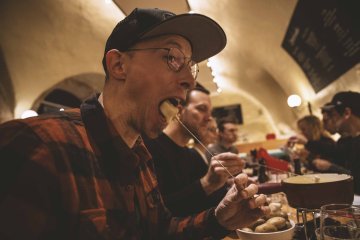