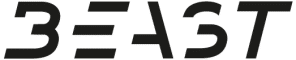
Composants en carbone High-End pour ton vélo, Made in Germany
BEAST Components est une jeune entreprise basée à Dresde, en Allemagne, qui s'est pleinement engagée dans le matériau carbone. Derrière BEAST se cachent des vététistes passionnés qui mettent leur savoir-faire dans la construction légère et le carbone avec le professionnalisme d'ingénieurs expérimentés dans le développement et la production de composants exceptionnels pour le vélo. Et le résultat est tout simplement spectaculaire.
Nous avons pu constater par nous-mêmes la production de haute qualité de guidons, potences, roues, selles et tiges de selle sur place à Dresde. La manufacture de carbone est située dans la zone industrielle au nord-est de la capitale saxonne et on peut le sentir dès qu'on entre dans le bâtiment : Ici, passion et professionnalisme vont de pair.
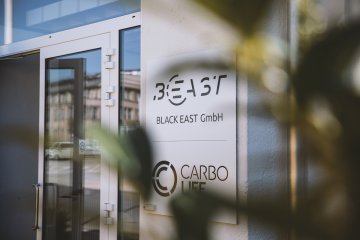
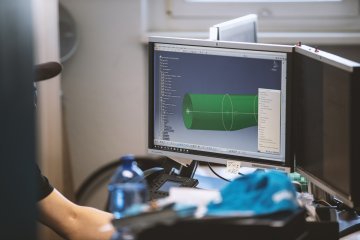
Les dirigeants et fabricants de BEAST Components, en particulier Mirko Filler, ont étudié et travaillé à l'Institut pour la construction légère de l'Université technique de Dresde avant de créer leur propre marque. Au cours de cette période, ils ont mis en œuvre une grande variété de projets pour les industries automobile et aérospatiale, et les composants qu'ils développent et produisent pour vélos bénéficient maintenant de cette expérience. "Ce qui m'a le plus fasciné, c'est la constance avec laquelle les méthodes scientifiques sont utilisées pour exploiter de manière optimale les propriétés exceptionnelles des fibres de carbone pour les produits.", explique Christoph, qui était sur place pour nous. "Grâce à leur approche scientifique de la construction des composants, ils peuvent aller jusqu'aux limites de ce qui est physiquement faisable, car ils savent très bien où se situent ces limites. Le résultat est un guidon idéal ou une roue dont le poids, l'esthétique et la meilleure sécurité possible sont parfaitement équilibrés.“
Et cette qualité de production se traduit par des composants irréprochables : Le guidon, les jantes ou les tiges de selle sont uniquement polies, de sorte que les structures fibreuses à partir desquelles les produits sont fabriqués sont clairement visibles. Cette méthode est d'une honnêteté impitoyable et ne permet aucune erreur lors de la stratification. You see what you get – Tu peux voir à ton guidon la précision avec laquelle les couches sont construites et la manière propre et précise, pour ne pas dire l'amour du détail, avec laquelle on travaille ici.
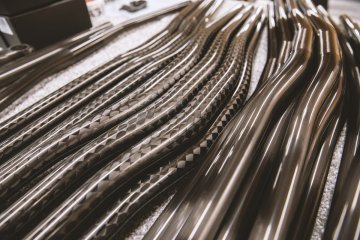
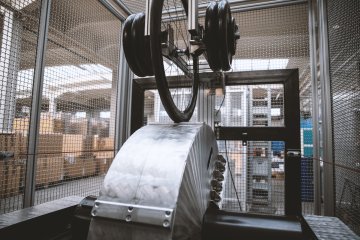
Mais avant que les pièces soient mises en forme, elles ont fait l'objet d'un long processus allant de l'idée initiale à la construction du prototype. Avant même que les premiers échantillons sortent d'un moule chez BEAST Components, les propriétés de résistance et de déformation des composants sont testées dans des simulations complexes par la méthode Finite-Elements. De cette façon, il est possible de calculer dans les moindres détails comment les produits sont fabriqués, comment les différentes couches de fibres de carbone doivent être posées afin d'obtenir le meilleur rapport poids/stabilité, flexibilité/amortissement possible. "Nous savons déjà avant même le test pratique sur nos bancs d'essai que nos composants tiendront le coup ", dit Mirko avec la confiance tranquille de ceux qui savent exactement ce qu'ils font et ce dont leurs produits sont capables. Ce ne sont pas seulement ses propres bancs d'essai qui lui montrent au quotidien les contraintes auxquelles les composants peuvent résister sans dommage. Des instituts d'essais indépendants tels que l'Institut Zedler à Ludwigsburg ou EFBE Prüftechnik GmbH à Walltrop confirment également la sécurité des produits BEAST, qui sont également homologués pour les vélos de downhill.
La production de composants prêts à l'emploi en série s'effectue alors avec une précision absolue seulement quelques mètres plus loin, Tout d'abord, les différentes couches sont coupées par ordinateur. Selon le produit, ils sont fabriqués soit dans le processus Prepreg-Autoklav, dans lequel les structures fibreuses pré-imprégnées et refroidies sont déposées dans le moule couche après couche selon un plan de construction précis, après quoi ils sont durcis en autoclave sous température et pression. Ou en Resin Transfer Moulding (RTM), dans lequel les structures de fibres sèches sont placées dans le moule dans l'ébauche appropriée et selon le plan de construction. Dans le processus d'injection suivant, ils sont trempés avec de la résine et durcis par la chaleur. La stratification, c'est-à-dire la mise en place des différentes couches de carbone, exige de la précision, de l'expérience et de l'habilité, car c'est ici que se construisent fibre par fibre, couche par couche, le guidon ou la roue.
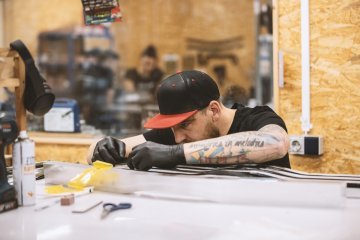
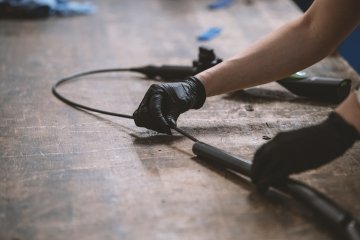
Après durcissement, chaque produit est minutieusement testé. Avec un endoscope, par exemple, le guidon est également examiné à l'intérieur pour détecter des défauts ou des irrégularités. Seuls des composants parfaits du point de vue de la construction sont ensuite envoyés au contrôle de la qualité optique, où les défauts mineurs sont retouchés. Les produits avec une structure en carbone optiquement défectueuse, avec des bulles ou des bosses sont éliminés ici. „Nous clients attendent des composants parfaits en tout point, et nous ne voulons pas les décevoir.", tel est le crédo de Mirko.
Notre visite chez BEAST Components nous laisse totalement convaincus qu'avec cette marque, nous pouvons t'offrir des composants en carbone d'une qualité exceptionnelle, qui sont à la fois légers et confortables, tout à la fois stables et sûrs. Une garantie du fabricant de 5 ans et le remplacement à vie pour premier propriétaire (50% de rabais sur le prix de vente conseillé) témoignent de la confiance accordée à leurs propres produits. L'engagement de Christoph envers BEAST Components n'est donc pas une surprise :
"Pendant longtemps, je n'ai conduit que de l'aluminium que pour des raisons de sécurité liées au carbone. Après ma visite chez BEAST Components, je dis maintenant : un guidon en carbone bien construit est plus sûr qu'un guidon en aluminium. Je fais confiance aux composants de BEAST."
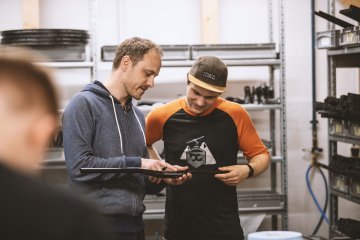
Premières impressions de notre visite chez BEAST Components
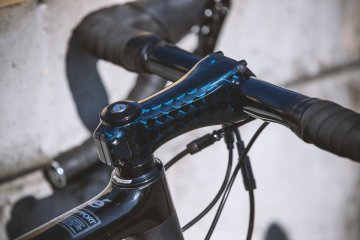
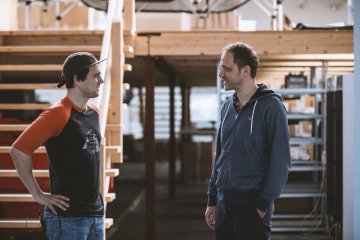
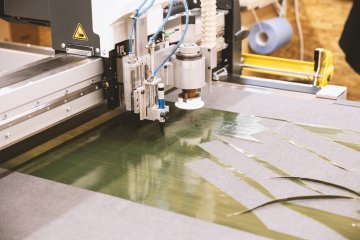
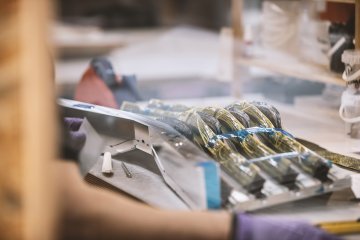
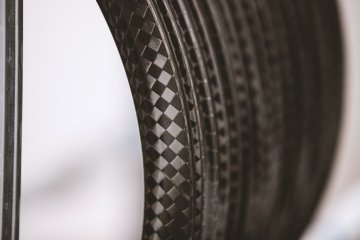
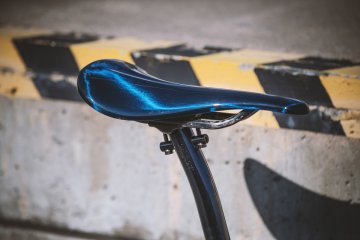
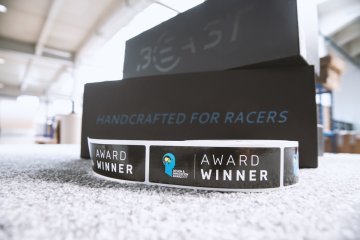
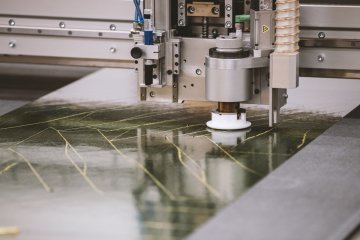
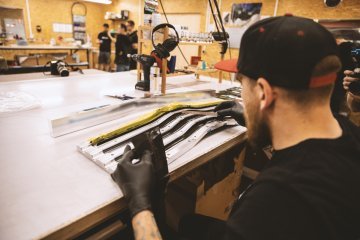
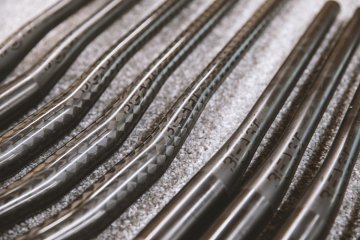
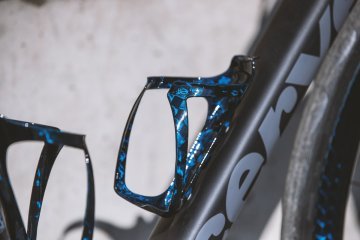
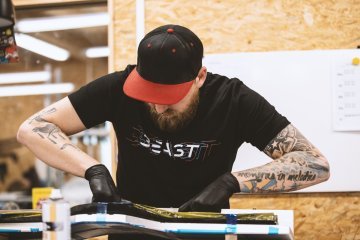
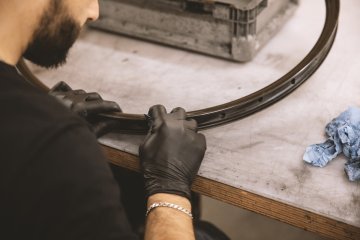
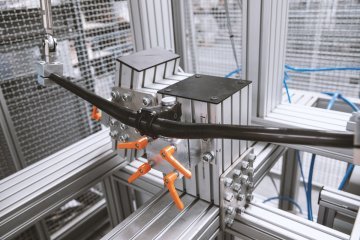
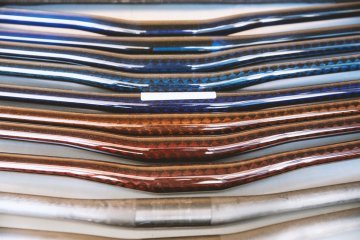